Seamless supply chain solutions for bulk materials
Bulk Materials
Modernising and optimising bulk materials handling processes and equipment are vital in keeping operations competitive. It takes knowledge of the granular details to keep bulk materials moving.
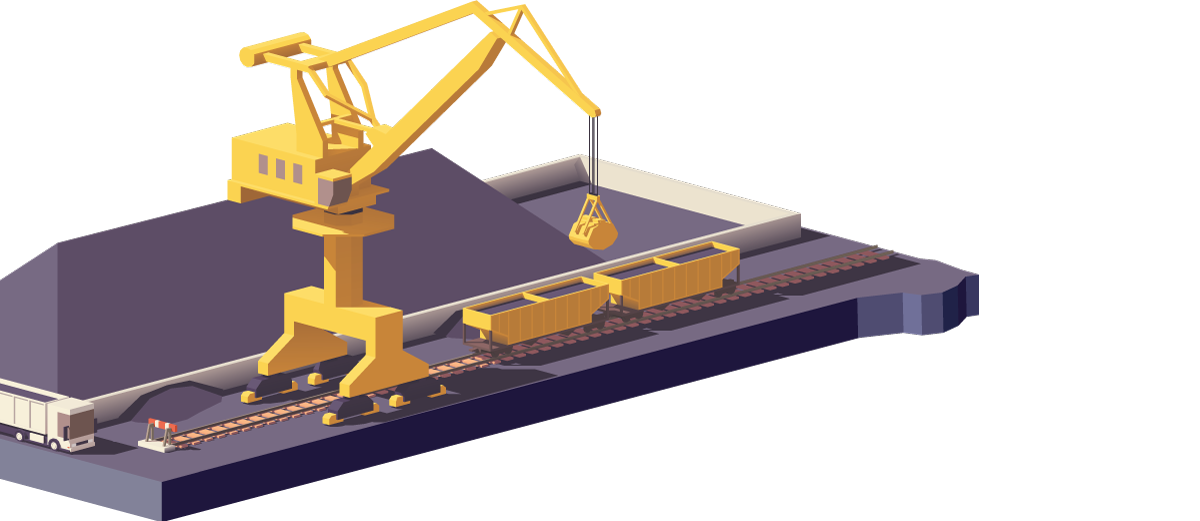
The challenge
Bulk materials handling systems should be straightforward: from extraction to processing, stockpiling, and loading onto transport, the bins, conveyors, chutes, feeders, hoppers, silos and other equipment are problem solvers, not problem creators.
Yet, these pieces of equipment and machinery that are the vital linkages between resource extraction, processing, and transport to the customer, can become bottlenecks or sources of inefficiency. Bulk materials systems face several issues, from suitable performance that enables the maximum volume of materials to be moved without impacting product quality, causing waste or spillage, to problems with reliability and safety, such as spillage and waste, difficulty in maintenance, or poor integration with other plant and equipment.
Increasingly, more modern quality control systems and process automation are allowing operators to track and manage material movement and quality to achieve greater efficiency and meet customer specifications, as well as reducing environmental impacts. The bulk materials handling systems of the 21st century need a holistic, multidisciplinary approach to ensure your systems add value, and your operations remain competitive.
The Soto way
Soto engineers take a whole-of-system approach to design, building, and refining bulk materials handling processes equipment. With vast experience across a range of industries, Soto engineers employ analysis and modelling tools to design new processes, and optimise existing operations, with seamless integration. This includes working with your process and systems engineers to model and develop outstanding outcomes for your overall supply chain.
As well as understanding the linkages and connections in the bigger picture, Soto engineers are adept at the finer details. Their knowledge of materials behaviour, such as flow and separation, enables imaginative design and problem solving of materials handling issues that are a drag on productivity, safety and quality.
We're proud of this one
Like a giant fishing reel, the Soto-design belt reeler for a mine operator in Western Australia is providing an imaginative solution for replacing kilometres of overland conveyor belt in a harsh climate and rugged terrain. To make the belt-replacement process more effective, efficient, and safe, the key requirement was for a piece of equipment that was modular, for ease of transport over long distances, and could store long lengths of belt to reduce the number of splices in the replacement belt.
Using 3D modelling and visual design tools, Soto engineers designed, built, and refined a modular belt reeler that sits astride the conveyor, winding up to 1.5 kilometres of belt onto each reel. The belt reeler is powered by a hydraulic drive control system, enabling the belt to wound up at constant tension to avoid piling up or tears, regardless of the width of the belt and gradient of the terrain, and each reel can be easily removed and loaded onto transport. The operator also has control over speed and tension to accommodate a variety of belt materials. The belt reeler has been a success, with close to 9 kilometres of conveyor belt already replaced, with zero faults reported.