
SOTO Consulting Engineers were on site recently to witness the trialling, commissioning, and handover of the new luffing radial stacker for their client Hanson Australia’s new Bass Point Quarry project. SOTO was engaged in the engineering and detailed design of several areas of the new plant, including the luffing radial stacker conveyor.
The Bass Point Quarry south of Wollongong has been a major supplier of high-quality basalt material for more than eight decades. Operated by Hanson, the quarry at Bass Point recently completed a $100 million expansion to increase production from 1.5 metric tonnes per annum (mtpa) to 4.0 mtpa.
New structures and ancillary equipment (photo gallery below) include the dual-lane truck out-loading building, pugmill, luffing radial stacker conveyor, power pack, and chutes. With the equipment commissioning 100% successful, the quarry has begun dispatching product from the new facility destined for the local and Sydney construction materials markets.
SOTO’s team of engineers and designers delivered on the promise, and bulk-materials handling equipment that is robust and efficient in the tough and rugged operating environment of the quarry has now been deployed.
For SOTO, it has been a privilege to work with Hanson to create bulk-materials handling solutions to meet the operational requirements of this quarry for its predicted 50-year life. SOTO is extremely proud of the outstanding engineering design capabilities deployed at this project, as well as the solid team effort that has helped ensure the best results for our clients.
SOTO was originally approached because of their well-earned reputation for in-house bulk-materials handling, mechanical engineering, and structural engineering. With SOTO on board, the client had the assurance that the equipment and machines required for this quarry would be designed with operational and safety parameters given the highest importance. For optimisation, Discrete Element Modelling (DEM) methods were used extensively by the SOTO team in the design of the transfer chutes and conveyors to ensure that the crushed material flows freely.
SOTO’s team of engineers and designers delivered on the promise, and bulk-materials handling equipment that is robust and efficient in the tough and rugged operating environment of the quarry has now been deployed.

Pugmill Shaft – Side doors open

Luffing Radial Stacker 1300TPH – 110kW for crushed rock.

Luffing Radial Stacker 1300TPH – 110kW for crushed rock.
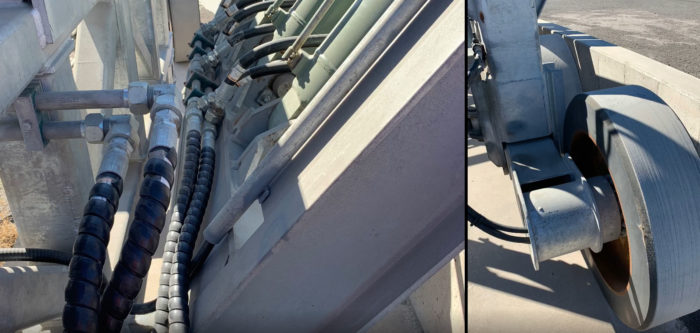
Hydraulically driven wheels and luffing cylinders
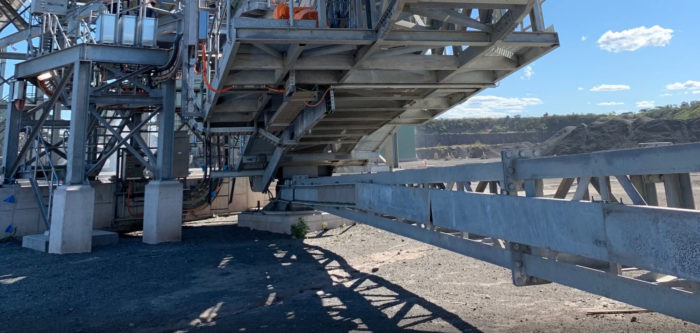
The underside of the Radial stacker drive platform and slew bearing.

Slew bearing of the luffing radial stacker conveyor
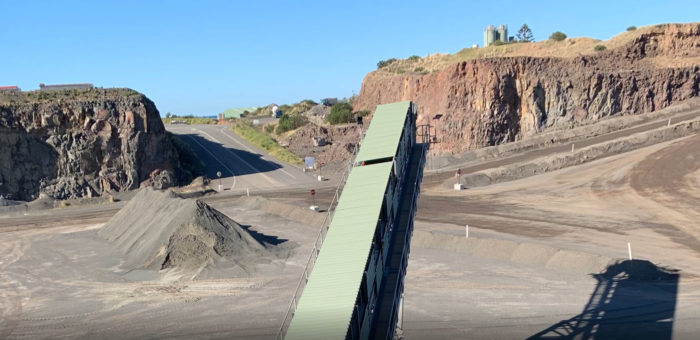
Luffing Radial Stacker 1300TPH – 110kW for crushed rock.
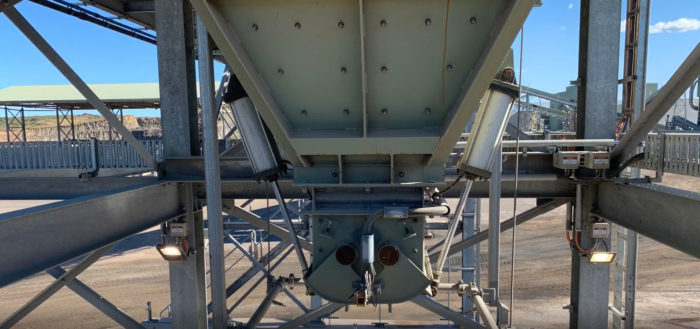
Truck Out loading – Bin No.1
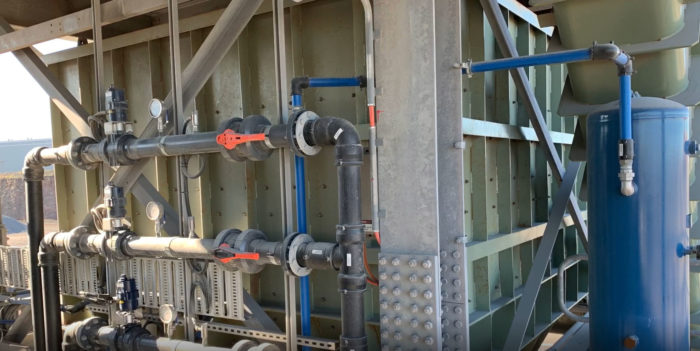
Load Out Bin. Water spray valves and piping in the foreground.
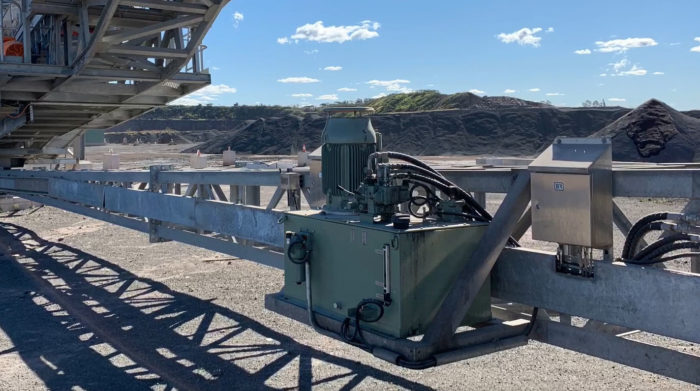
Hydraulic Power Pack for luffing and slewing of the stacker (designed & manufactured by Hydratech)
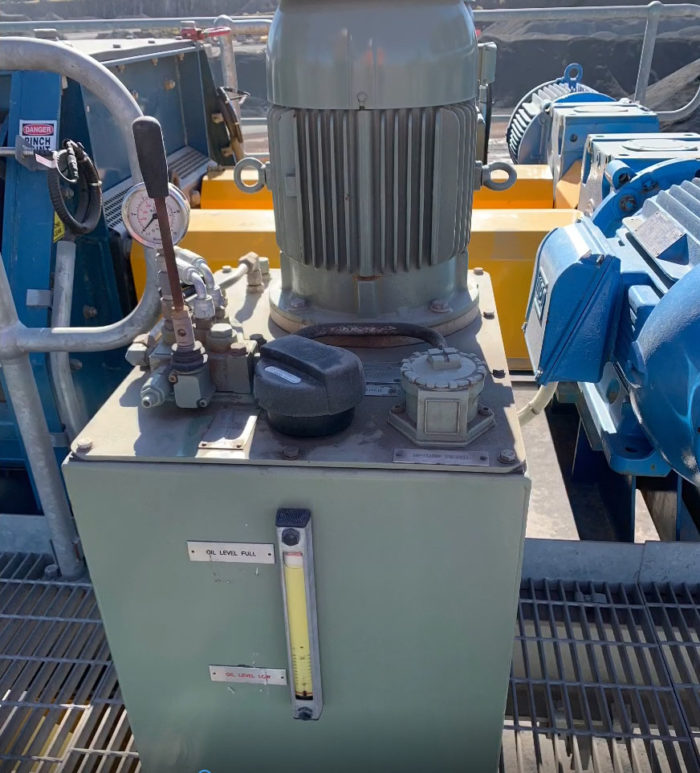
Power Pack for the Pugmill. Pugmill dual driveshaft in the background.

Load Out Bins – Load Cells for metering of crushed rocks into the trucks
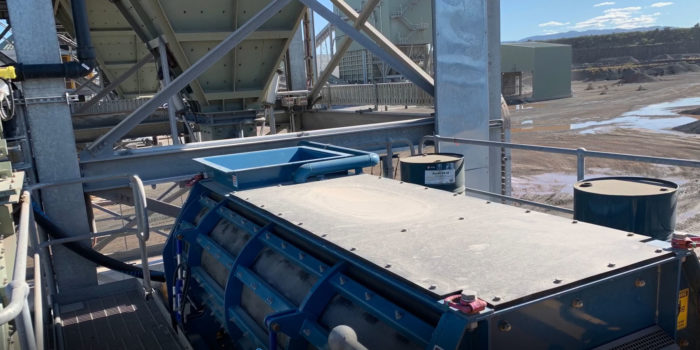
Pugmill in the foreground (manufactured & supplied by Rocktec)

Pugmill Shaft – Side doors open

Inlet of the PugMill
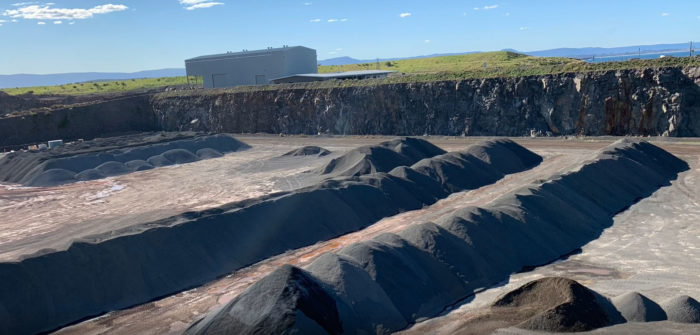
Sized Crushed Rock stockpiles 6mm to 50mm
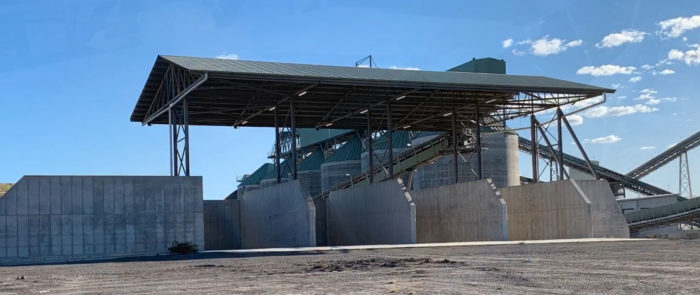
Crushed Rock Pre-Coat Plant – Radial stacker in the background.