customer story
Life Extension of BlueScope Steel Blast Furnace
A major project to extend the life of a blast furnace at BlueScope Steel Limited provided another significant platform for the Soto team’s rare talents in collaborative innovation and advanced engineering.
BlueScope operates Australia’s largest steelmaking facility at Port Kembla, in the heart of the sprawling Illawarra region south of Sydney. The centre of the steelworks operation thrums with a blast furnace making the iron from which the steel is produced. The furnace is essentially a huge steel shell structure. The giant shell is protected from the intense heat of the furnace by a combination of copper and cast iron staves through which water is circulated, forming an internal refractory lining. Each copper stave can weigh up to 3.5 tonnes, and can be as large as 3.5m x 2m. Over time, these staves wear out and the water circulation is depleted, requiring temporary shell cooling methods to be used. However, these alternative cooling methods are less effective than the water-circulating staves, causing the furnace wall temperatures to rise. Consequently, furnace production drops.
The magnitude of this situation cannot be understated: if the blast furnace stops manufacturing iron, steel production at Port Kembla would grind to a halt.
During the 3rd campaign of Blast Furnace No. 5, it was found that the staves were deteriorating at a much higher rate than anticipated. The risk of associated damage to the furnace made it critical that BlueScope find a solution. BlueScope initiated a major project that required exceptional ingenuity as the staves were to be replaced from outside the furnace, avoiding the need to shut it off.
The size of the project meant that it would span several years. A massive amount of pre-planning, engineering, and manufacture was involved. For example, the copper staves take approximately 9 months to be manufactured and delivered, and a minimum of 12 months of engineering and planning were necessary prior to the first stave replacement shutdowns.
During each shutdown event, the blast furnace burden would be run down to a minimum level and maintained by its residual heat for 5 days until reactivated. There was no flexibility about these 5 days: it was imperative that, during this period of furnace shutdown, the staves be removed and replaced using unique handling equipment that was carefully designed by Soto to suit the constraining conditions. These conditions included limitations of the access areas, lack of clear visibility, heat that rose up to 350°C inside the furnace, and the necessity of working at a height.
This set of conditions made the BlueScope blast furnace project work extremely specialised, demanding an innovative and collaborative work methodology and rigorous engineering design.
Just as important was building close work relationships with the BlueScope teams, so that everything worked like clockwork when the personnel replaced the staves while remaining outside the furnace, beating the clock every time to meet the absolute completion date.
At the conclusion of the BlueScope blast furnace project, the Soto team completed a celebratory summary of the factors that led to project success. These included:
- Accurate and innovative design engineering and stave replacement methodology.
- Detailed planning.
- Safety built into all project phases.
- Close collaboration with the client.
- An effective team approach that built invaluable relationships between key BlueScope personnel and Soto’s design engineers.
The winning elements above can be more simply described with Soto’s revered motto: Everything Engineered.
Scope of Soto’s Work
- Review of existing information covering the furnace design and previous stave replacement projects.
- Engineering design and stave replacement methodology.
- Design for temporary works and construction lifts.
- Documentation of design and replacement methodology.
- Safety reviews and design of equipment to facilitate stave replacement.
- Detailed engineering support throughout trials and execution of the project including:
- Hands-on site supervision and problem solving in close collaboration with key BlueScope staff
- Back office engineering design, modelling and calculations.
Why Soto?
- Shutdown brownfield engineering experience and successful track record.
- Organisational memory of previous stave replacements at BlueScope Steel.
- Successful track record of working collaboratively with BlueScope personnel.
- Ability to provide in-house integrated concept-to-detailed multi-disciplinary engineering comprising mechanical, structural, advanced computation analysis and expert knowledge of finite element analysis (FEA), 3D modelling, and drafting.
- Lift design for heavy loads in constrained brownfield site conditions where only minimal disruption to operations can be tolerated.
- Provision of practical on-site and hands-on engineering support during the construction phase.
How? The Detailed Snapshot of Soto’s Success on the Project
The project structure staged stave replacement into specific areas within the furnace, each having tailored procedures and equipment to complete the works. In general, each area had the following stages:
Stage A: Research and Development, Engineering and Initial Trials
- Review of existing information including:
- Information on proposed stave replacement methodology from BlueScope’s blast furnace personnel.
- Existing 3D inventor model of the furnace.
- Existing drawings, technical specifications, and calculations.
- Information on the proposed cooling system modifications that will affect the stave replacement methodology.
- Mechanical engineering design of equipment and construction aids required for the stave replacement project, and continual development of 3D Master model.
- Structural modifications to facilitate safe access during shutdowns, including new and temporary platforms, lifting beams, and movement portals through structure.
- Client deliverables included 3D Inventor Models and drawings, AutoCAD drawings and Calculation reports.
- Design and execution phase methodology reviews: Optioneering to assess alternative methods of stave replacement, technical design reviews, safety in design reviews, integrated risk analyses. and stave replacement safety reviews.
- On site simulations were designed and constructed to trial the stave replacement methodology, construction aids, and train the work crews. In conjunction with BlueScope’s engineers, these shutdowns were used to assess the equipment and processes, facilitating modifications to the methodology prior to the major shutdowns.
- Small scale stave replacement was carried out during planned minor shutdowns. This allowed re-assessment prior to extensive stave replacement in stage B (below) during a later major planned shutdown.
Stage B: Major shutdowns
- On-site engineering during major stave replacement shutdowns, including hands-on supervision and problem solving in conjunction with BlueScope engineers.
- Stave replacement.
- Post shutdown engineering reviews to determine what was learned and where process improvements could be made.
- Engineering to redesign or develop new equipment and procedures based on above for future major shutdowns.
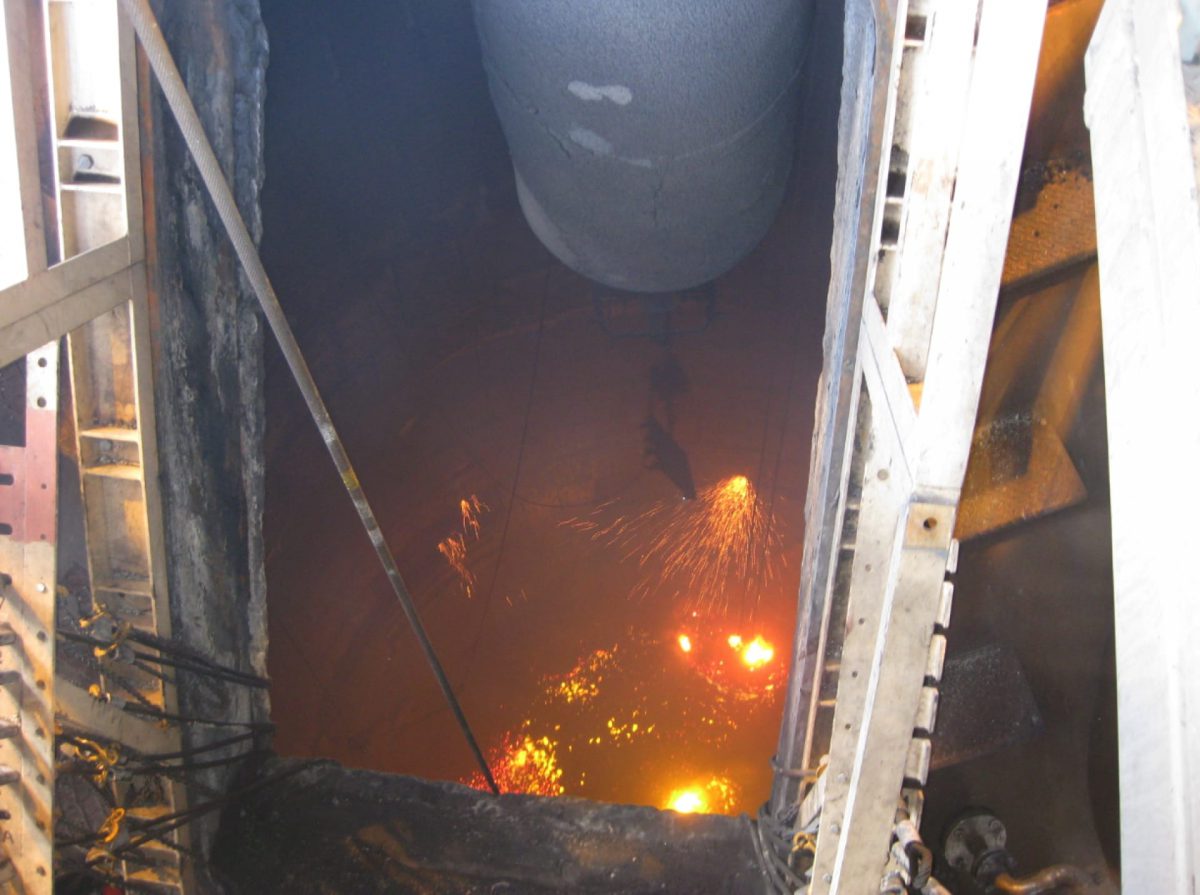
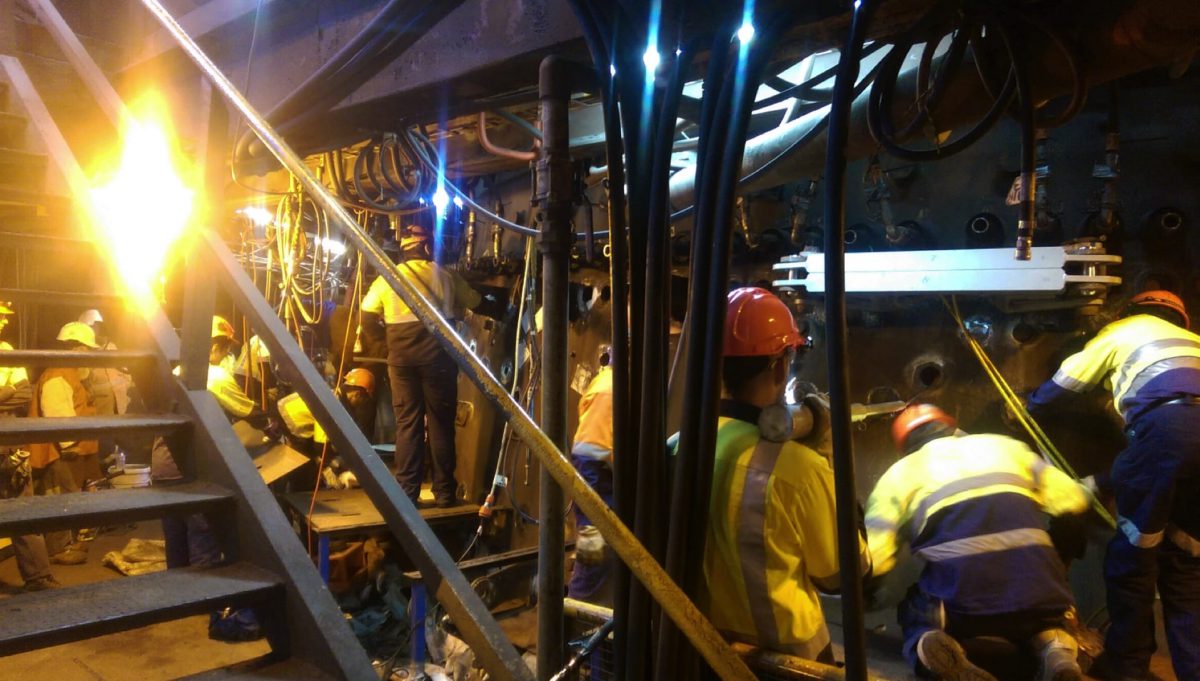
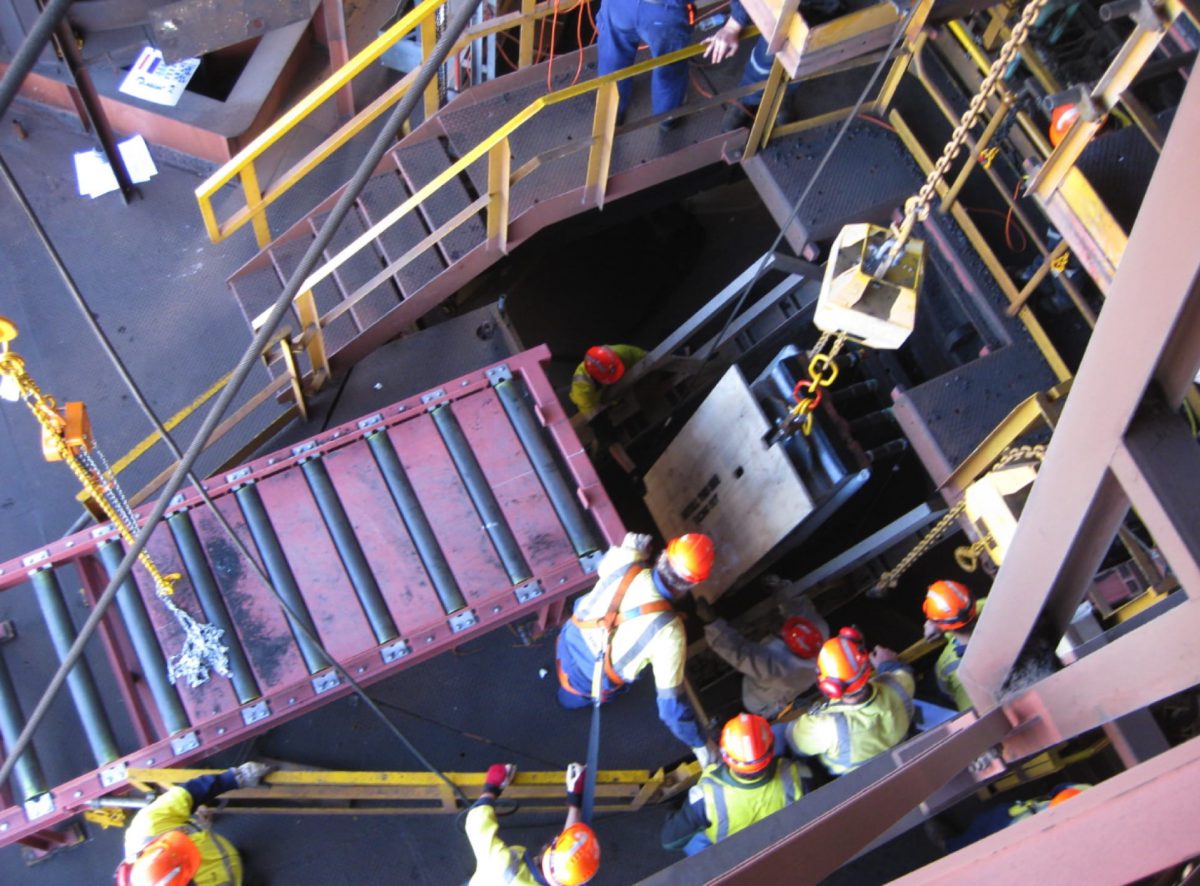
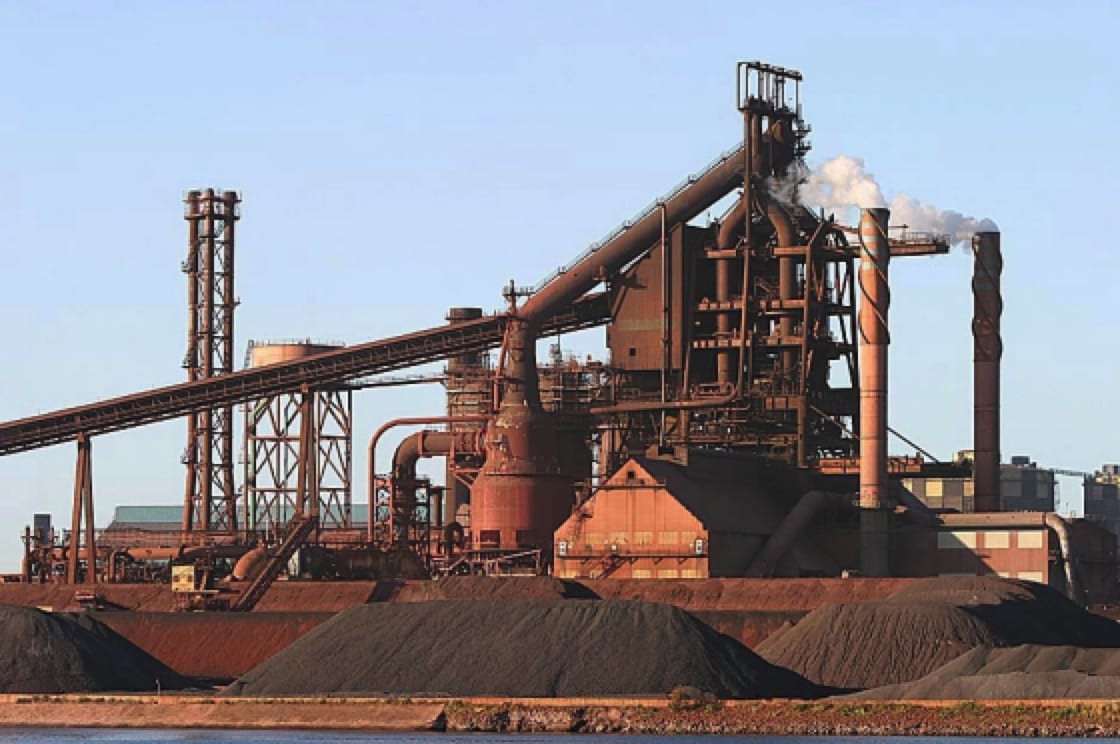
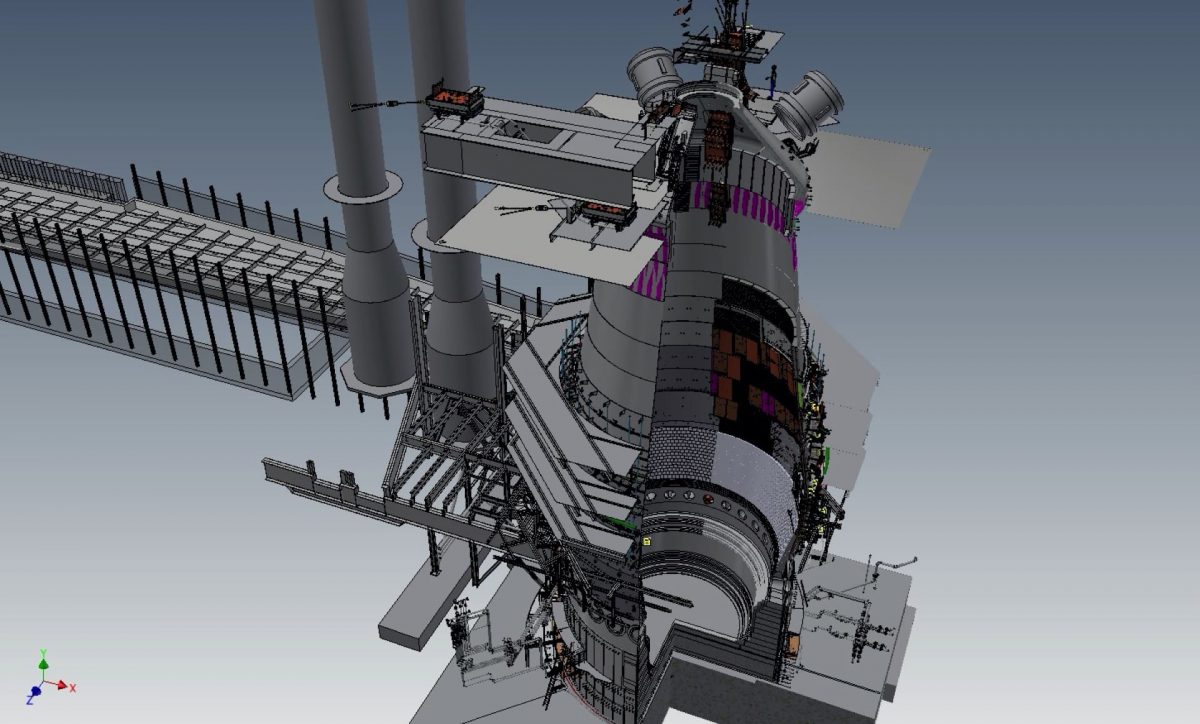